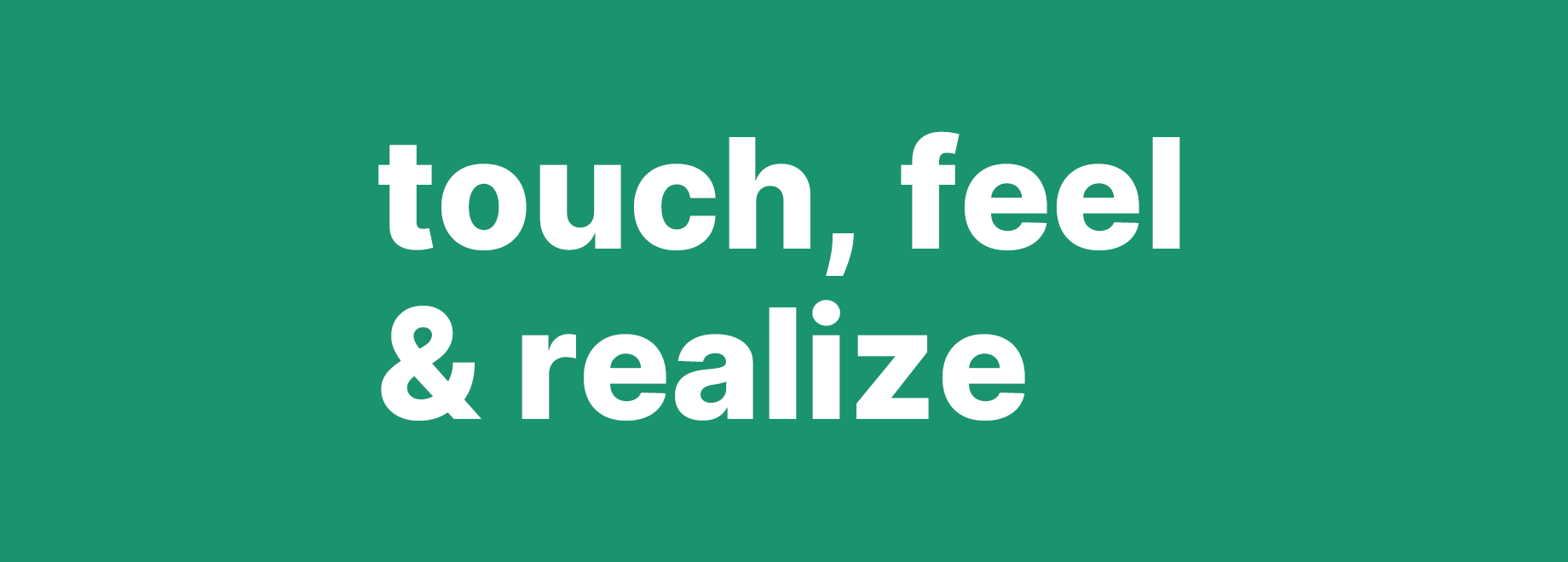
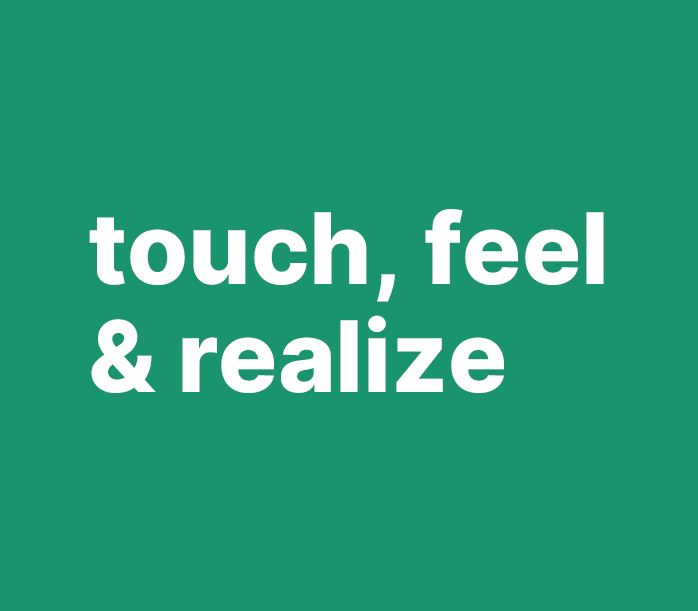
Prototyping
We are engaged in multiple proof of concept and innovative design efforts. For us, a good place to start would be with an early-stage concept that needs to be validated and turned into a product.
Proof-of-Principle Prototype
A Proof of concept prototype is used to test some aspect of the intended design without attempting to exactly simulate the visual appearance, choice of materials or intended manufacturing process. Such prototypes can be used to “prove” out a potential design approach such as range of motion, mechanics, sensors, architecture, etc. These types of models are often used to identify which design options will not work, or where further development and testing is necessary.
Form Study Prototype
This type of prototype will allow designers to explore the basic size, look and feel of a product without simulating the actual function or exact visual appearance of the product. They can help assess ergonomic factors and provide insight into visual aspects of the product’s final form. Form Study Prototypes are often hand-carved or machined models from easily sculpted, inexpensive materials (e.g., urethane foam), without representing the intended color, finish, or texture. Due to the materials used, these models are intended for internal decision making and are generally not durable enough or suitable for use by representative users or consumers.
User Experience Prototype
A User Experience Model invites active human interaction and is primarily used to support user focused research. While intentionally not addressing possible aesthetic treatments, this type of model does more accurately represent the overall size, proportions, interfaces, and articulation of a promising concept. This type of model allows early assessment of how a potential user interacts with various elements, motions, and actions of a concept which define the initial use scenario and overall user experience. As these models are fully intended to be used and handled, more robust construction is key. Materials typically include plywood, REN shape, RP processes and CNC machined components. Construction of user experience models is typically driven by preliminary CAID/CAD which may be constructed from scratch or with methods such as industrial CT scanning.
Visual Prototype
Visual prototype will capture the intended design aesthetic and simulate the appearance, color and surface textures of the intended product but will not actually embody the function(s) of the final product. These models will be suitable for use in market research, executive reviews and approval, packaging mock-ups, and photo shoots for sales literature.
Functional Prototype
A functional prototype, also known as a working prototype, will make every effort to replicate the desired design’s final appearance, feel, and components as closely as possible. To cut expenses, the working prototype might be scaled down in size. Before ordering bigger production runs, engineers can make last-minute adjustments and check for design problems by building a completely functional full-scale prototype, which serves as the ultimate test of concept.
Let’s work together!
Transform your brand experience from commencement to delivery with solutions that resonate on a grand scale.